BM TRADA’s frameCHECK✔timber frame consultancy specialists inspect and report on timber frame elements to help ensure that your building is being constructed in accordance with the specification and best practice.
What is timber frame construction?
Timber frame is a method of construction. It is not a system of building, although there are a number of well researched systems which use timber frame as a basis.
Timber frame construction uses timber studs and rails, together with a structural sheathing board, to form a structural frame which transmits all vertical and horizontal loads to the foundations.
Platform frame is the most commonly used method in the UK. Each storey is framed with floor-to-ceiling height panels and the floor deck of one floor becomes the erection platform of the next.
frameCHECK✔ timber frame consultancy services
BM TRADA's frameCHECK✔ timber frame consultancy service specifically looks at:
- Timber frame detailing
- Durability
- Fire resistance
- Acoustic performance
- Thermal performance.
And includes:
- Timber frame training
- Timber frame publications
- Design detail evaluation
- Site inspections
- Defect and remedial consultancy.
frameCHECK✔can be carried out during the construction process, or on completed or stalled projects, giving you assurance that the timber frame building you have commissioned is being built correctly and to your requirements. This specialist service aims to help improve the quality of build, reduce call backs and confirm compliance.
Who would benefit from frameCHECK✔ timber frame consultancy?
- Affordable housing providers
- House builders
- Developers
- Warranty and control bodies
- Architects.
Benefits of frameCHECK✔
- Improve quality – an expert pair of eyes overlooking the build process
- Increase performance – suggest best practice details to exceed current regulations
- Save money – identify efficient construction methods and order of work
- Reduce call backs – train people how to do a job right first time
- Demonstrate compliance – assess materials and building systems against standards.
Your timber frame construction FAQs answered
If you cannot find the answer to your query below, please contact our free Timber Technical Helpline (Mon-Fri 9-5pm) on 01494 840 774 for further advice.
Our Services
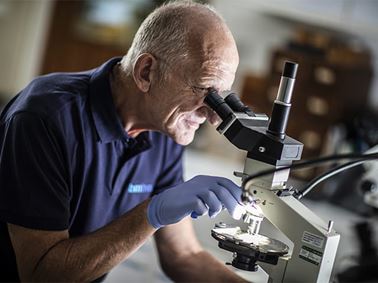
Other Timber Inspection Services
BM TRADA has a long history of providing consultancy on a wide range of timber products and services.

Timber Preservative Testing
BM TRADA offers timber preservative testing of treated wood using test methods and protocols from relevant British and European Standards to establish whether treatment levels in wood samples have been met at the time of treatment.
Related Information
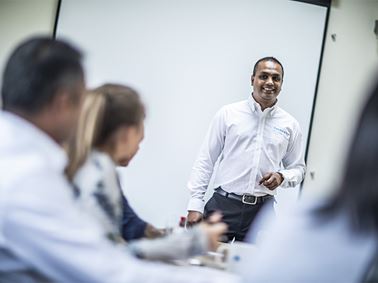
Timber Training
Our experts provide a range of courses from visual strength grading through to scaffold boards and timber frame construction.
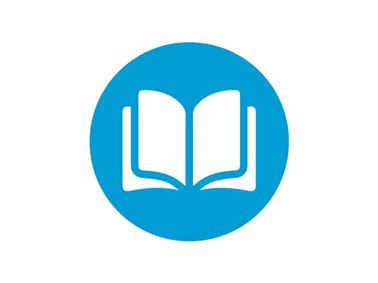
Training Courses
BM TRADA provides a range of training courses. Our training portfolio includes timber, fire, management systems, chain of custody, sustainable supply chain and business training.
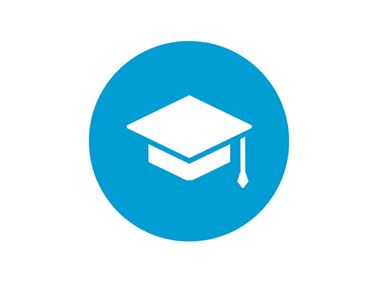
Training Booking
Download our Training Booking Form.
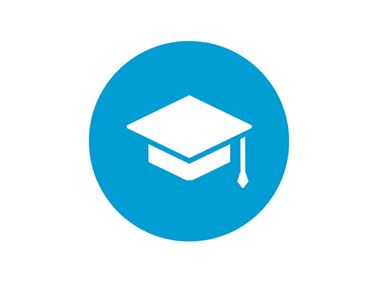
Training Terms and Conditions
Read the Training Terms and Conditions.
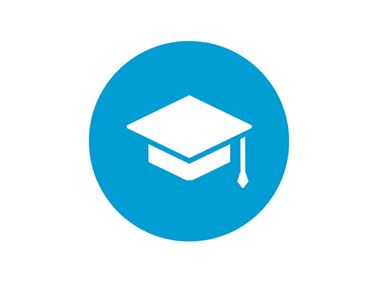
Course Directory
Download our current Training Course Directory to discover more about our wide range on offer.
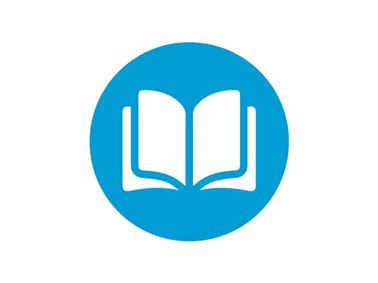
Articles and Blogs
Access our library of technical articles and blogs to help you better understand our services and how we can help you.